Data Acquisition Is Essential in Control System Integration
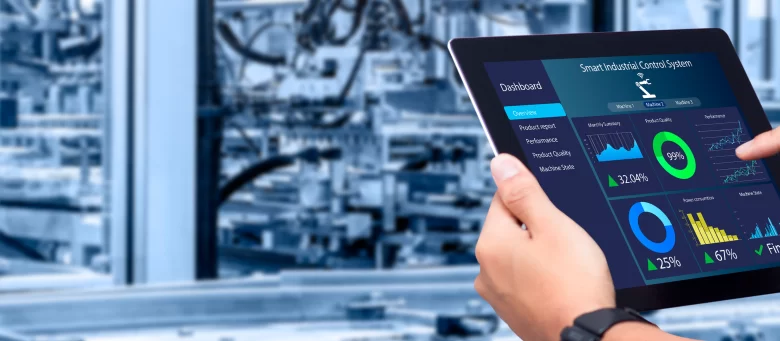
In today’s world of complex industrial systems, data acquisition plays a pivotal role in ensuring smooth operations and optimal performance. Control system integration relies on accurate, real-time data to make informed decisions, maintain system efficiency, and avoid costly downtime. But what exactly makes data acquisition so essential for these systems? Let’s dive into why it’s a key component in control integration and how it benefits different aspects of system performance.
Capturing Real-Time Metrics for Informed Decision-Making
When it comes to managing complex systems, having access to real-time metrics is a game-changer. Data acquisition allows a control system integrator to capture real-time information from multiple sources, whether it’s temperature, pressure, or flow rates. This real-time data gives operators the ability to make quick, informed decisions that can prevent problems before they escalate into bigger issues.
Imagine a scenario where a machine’s temperature spikes suddenly. With real-time data acquisition, the system can immediately alert operators, allowing them to take corrective action before any damage is done. The more accurate and immediate the data, the quicker decisions can be made, ultimately leading to safer and more efficient operations.
Enabling Accurate System Calibration and Fine-Tuning
Accurate system calibration is essential to ensure everything operates within desired parameters. Data acquisition provides the foundation for this by collecting critical information that allows a controls integrator to calibrate systems with precision. Without the correct data, it becomes nearly impossible to fine-tune machinery or equipment to its optimal settings.
For example, if a piece of equipment is consistently running below its desired performance level, analyzing the data collected can help pinpoint where adjustments need to be made. Whether it’s tweaking pressure levels or adjusting temperature controls, data helps ensure that fine-tuning leads to the desired outcome, improving overall system efficiency.
Enhancing Predictive Maintenance Through Comprehensive Data Analysis
Predictive maintenance has become a cornerstone of modern industrial operations, and data acquisition is at the heart of it. By continually gathering data on system performance, a control system integrator can identify patterns that may indicate a component is nearing failure. This foresight allows for maintenance to be scheduled before a breakdown occurs, avoiding costly unplanned downtime.
Instead of waiting for something to go wrong, predictive maintenance lets companies be proactive, fixing problems before they arise. Through data acquisition, trends such as vibration irregularities, increasing temperatures, or changes in operational speeds can be detected early. This predictive approach not only extends the lifespan of equipment but also reduces repair costs and boosts overall productivity.
Supporting System Optimization with Detailed Performance Insights
Optimization is key in any industrial setting, and data acquisition is the driving force behind it. By analyzing performance data, a control system integrator can identify areas where improvements can be made to boost efficiency or reduce energy consumption. This process might involve fine-tuning control loops, reconfiguring settings, or even upgrading components.
With detailed insights into how every aspect of the system performs, operators can make informed choices about which processes to optimize. Continuous monitoring and analysis of real-time data provide a clear picture of the system’s strengths and weaknesses, allowing for strategic adjustments that lead to better outcomes, including higher productivity and lower operational costs.
Facilitating Troubleshooting by Tracking Historical Data Trends
Troubleshooting a problem in a complex system can feel like searching for a needle in a haystack—unless you have access to historical data trends. Data acquisition simplifies the troubleshooting process by providing a record of system behavior over time. This historical data allows a controls integrator to track the exact moment when a problem started and identify the potential causes.
By reviewing data trends, operators can detect patterns that may not have been noticeable during real-time operations. For instance, a slight change in pressure or temperature over a period of days or weeks might indicate an issue that could develop into a larger problem if left unresolved. With historical data in hand, troubleshooting becomes a more straightforward and efficient process, helping to minimize downtime and maintain system integrity.
Improving Process Control with Precise, High-Fidelity Data
Accurate data is the backbone of effective process control. For any control system integrator, the ability to gather precise, high-fidelity data ensures that every part of the system is functioning as intended. This high level of precision helps in making small yet impactful adjustments that keep processes running smoothly and efficiently.
When it comes to controlling complex processes, small inaccuracies in data can lead to significant deviations in performance. By using high-quality data acquisition tools, control system integrators can guarantee that their systems are getting the most reliable information possible. This helps in maintaining tight control over processes, reducing waste, and improving overall system performance.