Buying Concrete Grinding Diamonds: 6 Essential Factors
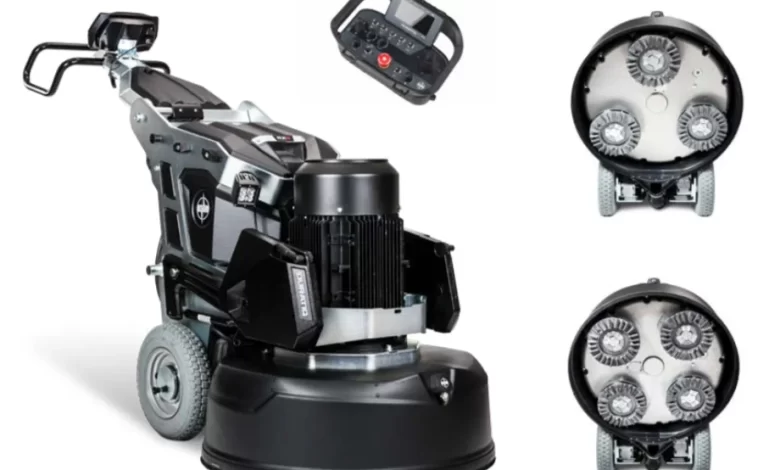
Concrete grinding plays a crucial role in construction and renovation by preparing surfaces for further work, such as polishing, coating, or leveling. It helps remove imperfections, old coatings, and uneven layers, ensuring a smooth, durable base. In recent years, the demand for high-quality finishes has grown significantly in both residential and commercial projects. Homeowners, architects, and businesses seek polished concrete floors for their aesthetic appeal, durability, and low maintenance. These finishes are now popular in homes, offices, warehouses, and retail spaces, highlighting the importance of precise and efficient concrete grinding in achieving the desired results.
Concrete grinding diamonds, also known as “floor grinding shoes” or “diamond grinding shoes” in the United Kingdom, Australia, and New Zealand, are essential tools for concrete grinding contractors. These tools enable contractors to complete their jobs efficiently and effectively, ensuring high-quality surface preparation and finishing.
Concrete grinding diamonds are specifically designed for use with floor grinding machines, ensuring high-performance grinding of concrete and terrazzo floors. With the increasing demand for high-quality finishes in both residential and commercial applications, understanding the various options available is crucial. Given the wide variety of floor grinders on the market—each featuring different connection systems and holder plates—many types of concrete grinding diamonds are tailored to suit different machines, including popular brands like HTC, Husqvarna, Lavina, ASL, Klindex, and more.
When buying concrete grinding diamonds, it’s important to keep six key factors in mind to ensure you make the right choice:
1. Machine Compatibility:
This is one of the first factors to consider when selecting concrete grinding diamonds. While some floor grinding machines may use similar diamond tooling, such as trapezoid grinding shoes, many machines—especially from well-known brands like HTC, Husqvarna, Lavina, and Klindex—require specific, proprietary tooling. These brands design their products to be unique and non-interchangeable with other machines, which helps maintain product exclusivity. However, there is a solution to overcome compatibility issues: adaptor plates. By using an adaptor, you can make different types of concrete grinding diamonds compatible with the same machine, allowing for greater flexibility without the need to buy new tooling for every machine type.
2. Segment Shapes:
The shape of the diamond segments significantly influences how aggressively the tool grinds. Classic segment shapes include round, rectangular, and trapezoidal. Round segments are generally used for smoother grinding and polishing, while rectangular and trapezoidal segments offer more aggressive cutting, making them ideal for removing coatings or heavy material. Understanding the right shape for your specific application can greatly enhance efficiency.
3. Segment Heights: Segment height refers to the thickness of the diamond segment, impacting both the tool’s lifespan and cost. Taller segments generally provide longer durability due to containing more diamond material, which justifies their higher price. They also allow for a finer finish on tougher surfaces. When comparing concrete grinding diamonds from different suppliers, be sure to consider segment height as a crucial factor in your decision-making process.
4. Segment Numbers:
The number of segments on a grinding tool affects both the speed and finish of the grinding process. Fewer segments allow for faster, more aggressive grinding, but can leave a rougher surface. More segments lead to smoother results but require more passes, making them better suited for polishing or fine-grinding tasks. Additionally, more segments can help improve cooling during operation, enhancing the tool’s overall performance.
5. Diamond Grits:
The diamond grit size determines the level of coarseness or fineness in the grinding process. Lower grits (16-30) are used for initial grinding and surface preparation, where material removal is the primary goal. Higher grits (60-120) are designed for smoothing and polishing, ideal for achieving a fine finish on concrete or terrazzo floors. Transitioning from lower to higher grits during a project can help streamline your workflow and improve the final appearance.
6. Bond Types:
The bond type refers to the hardness of the metal holding the diamonds in place, which must be selected based on the hardness of the concrete you’re grinding. Softer bonds are better suited for hard concrete, as they expose fresh diamonds more quickly, while harder bonds are ideal for soft concrete to prevent premature wear. Additionally, consider environmental factors like temperature and humidity, as they can influence bond selection. Avoid common mistakes by matching the bond type to your specific grinding conditions.
By keeping these factors in mind, you can make an informed decision when purchasing concrete grinding diamonds. Selecting the right tools will not only enhance your grinding efficiency but also improve the quality of your finishes.
As an expert in manufacturing diamond tools, Xpert Diamond Tools offers a comprehensive guide to choosing the right concrete grinding diamonds. This guide includes the points mentioned above, along with our product list, OEM/ODM services, packaging methods, lead times, payment terms, and more. Visit us today to explore our resources and elevate your concrete grinding projects!